MTD Audiobook
Over 80% of the UK’s SMEs believe apprenticeships are at least partly the solution to the UK’s skills gap crisis, with a further 69% of the view apprenticeships are a ‘valuable alternative to university’ Four in 10 (44%) feel not enough is being done to encourage young people to consider apprenticeships. The findings are taken from the latest independent research commissioned by Close Brothers Asset Finance and are in support of National Apprenticeship Week (NAW), which highlights the positive impact that apprenticeships make on individuals, businesses and the wider economy....
info_outlineMTD Audiobook
Edging closer to its 50th anniversary, the Progressive Technology Group has enjoyed a meteoric rise over the last decade. Founded in 1977, the relocation to larger premises in 2013 was one of the many catalysts for the Newbury company’s decade-long growth. Opening multiple new divisions and branching into new markets, the company now employs more than 250 staff. Among its accolades are many prestigious awards from AMG Petronas and Rolls-Royce, to name a few. However, this pedigree cannot be bought; it is embedded in the company’s culture, with Progressive Technology opening its Apprentice...
info_outlineMTD Audiobook
The Brough Superior, a classic British motorcycle designed by George Brough in 1919 and manufactured in Nottingham, was of such high quality that it was dubbed the Rolls-Royce of motorcycles. One famous customer, T.E. Lawrence (Lawrence of Arabia), owned eight and died in 1935 from injuries sustained when he crashed number seven. The design was beautiful and practical, and a sidecar was often added. Although the factory closed after the Second World War, enthusiasts have ensured the name survives. In 2004, around 1,000 original Brough Superior motorcycles still existed. The brand is regularly...
info_outlineMTD Audiobook
Difficult-to-cut materials are defined as engineering materials with significantly lower machinability than typical. These materials are often referred to in shoptalk as ‘hard-to-machine,’ ‘tough-to-cut,’ or even ‘nasty.’ It is important to note that high hardness is not the only characteristic that makes these materials challenging to machine; several other factors contribute to their machining difficulties. Every industrial branch, in one way or another, must deal with such materials. However, the leading consumer of these materials is the aerospace industry. It is in this...
info_outlineMTD Audiobook
Building on the success of their award-winning 3D-printed stator bore tool for electric vehicle machining, Kennametal has developed an innovative 3D-printed transmission housing tool for Voith that cuts weight by approximately 45% and reduces machining time by approximately 50%. As transportation components become increasingly more sophisticated and the requirements more stringent, manufacturers need complex tooling solutions to machine those components. That poses a challenge as the weight of such tooling can become too heavy for efficient operation on machining centres, tool changers and...
info_outlineMTD Audiobook
The electrification transition and inflexible EV production quotas are taking a heavy toll on the automotive industry, but buses and commercial vehicles posted their best years since 2008. Will Stirling reports. MTD magazine is unwaveringly positive in its coverage of manufacturing news, but facts are facts: automotive manufacturing is on a downward slide. Combining cars and commercial vehicles (CVs), the UK produced 905,233 units in 2024, -11.8% from 2023, and slipping below the psychologically important one million units mark. Electric vehicles now comprise over one-fifth of all new car...
info_outlineMTD Audiobook
Opening its doors with just four toolmakers 50 years ago, Smithstown Light Engineering Ltd is now a business with three manufacturing sites and over 165 employees. Working with the world’s leading medical device and orthopaedic companies, Smithstown extensively uses OPEN MIND Technologies‘ hyperMILL CAD/CAM suite to streamline its throughput and maximise efficiency. Initially a toolmaking business supplying plastic injection moulds to the electronics industry, the Shannon-based business transitioned to medical manufacturing in 1990—and it hasn’t looked back since. With two sites in...
info_outlineMTD Audiobook
Michael Phillips, joint owner with partner Wayne Robins of contract machining firm Atomic Precision, describes their recently purchased, Japanese-built Brother Speedio U500Xd1 as ‘a Swiss army knife of 5-axis machining centres.’ His comment is due to the 30-taper machine’s high quality, versatile functionality, compactness, and ability to complete an extensive range of jobs quickly and efficiently. Brother machines are sold and serviced in the UK and Ireland by Whitehouse Machine Tools, Kenilworth. Founded in East Hendred, Oxfordshire, in 2020 by the two time-served mechanical...
info_outlineMTD Audiobook
Engines were already being built at the site in Zafra in 1875, where DEUTZ today has its main factory for processing engine components. Around 500 employees in modern manufacturing facilities produce engine blocks, cylinder blocks, connecting rods, and gears for the Group’s assembly lines in Cologne and Ulm. DEUTZ’s new 3.9-litre diesel engine is mostly used in agricultural and construction machines. It is designed for long service life as an industrial engine and will be built until at least 2035. Series production will start in the coming year after the current prototype phase....
info_outlineMTD Audiobook
Mills CNC has recently supplied Ayrshire Precision, a subcontract specialist based in Ayrshire, with two new SYNERGi systems. The systems, both derivations and highly customised versions of Mills’ standard SYNERGi ‘SPRINT’ solutions, were installed at Ayrshire Precision’s 14,000sq/ft site. In 2023, the first system was retrofitted to a Puma 2600SY lathe, and six months later, the second was retrofitted to a Puma 2100SY. SYNERGi Sprint automation systems are compact, flexible, and cost-effective. Mills’ dedicated automation experts can integrate them with DN Solutions’ lathes,...
info_outlineThe aerospace industry is experiencing unprecedented growth, driven by record demand for commercial jets, defence programmes and space exploration. To seize this opportunity, suppliers must find ways to ramp up output without compromising quality, innovation, or cost. By Will Stirling
The biggest hurdle facing the aerospace industry is how to scale up production. Airlines are investing heavily in new fleets, governments are increasing spending on advanced defence systems, and private companies are pushing the frontiers of space exploration and satellite technology. While this growth is a welcome rebound after years of turbulence, it has exposed bottlenecks in the supply chain, exacerbated by rising operational costs, material shortages and evolving regulatory requirements.
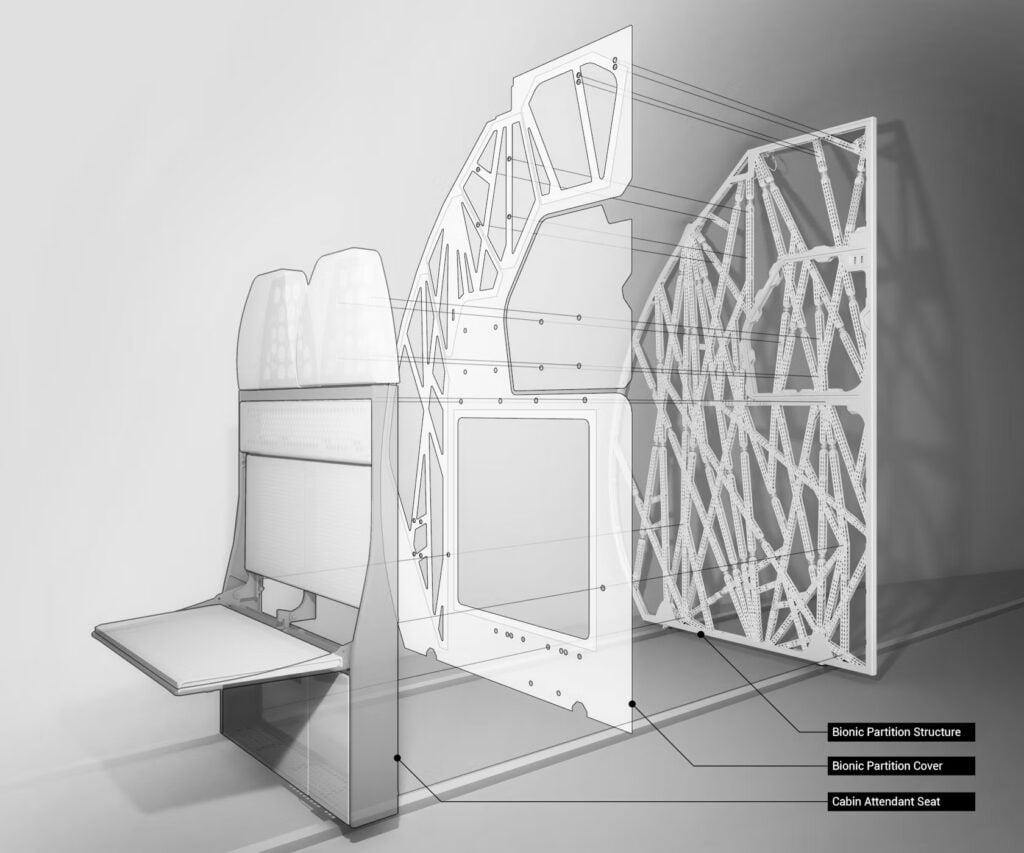
Nowhere is this challenge clearer than in the commercial aircraft backlog, which has ballooned to nearly 16,000 planes – valued at more than £250bn for the UK alone. At current production rates, clearing this backlog could take over a decade. Meanwhile, demand continues to climb as airlines place hundreds of new orders yearly.
Yet, this pressure brings opportunity. “The fact I can’t name another industry with a 10-year-plus backlog worth over US$1.5 trillion globally shows just how massive the growth trend is,” says Balaji Srimoolanathan, Director for Aerospace, Space and the Aerospace Growth Partnership at ADS.
“The primes and top tiers are diversifying their suppliers, sustainability is becoming ever-more critical, and new technologies are accessible and affordable. There is more business to be won by a greater number of suppliers than ever before, adding up to more opportunities, particularly for those with the right tools and technologies in place.”
Srimoolanathan explains that the key to unlocking these opportunities lies in integrating advanced capabilities, such as intelligent manufacturing systems, into today’s production processes. This move has been proven to drive greater efficiency and agility without comprising stringent quality standards.
Digital Innovation in Action
As production ramps up, shortages of critical components like semiconductors, electronics and raw materials like aluminium and titanium continue to cause delays. The pandemic’s ripple effects are still being felt, slowing assembly lines and affecting deliveries. Even seemingly minor components, such as fasteners, are in short supply.
Recognising this, LISI Aerospace partnered with the University of Sheffield Advanced Manufacturing Research Centre (AMRC) to explore how digital tools can drive process improvements. Together, they developed a cutting-edge smart production line at LISI’s Rugby facility.
The pilot line integrates five connected factory machines, each handling a distinct process. Key innovations include sensor data and data analytics to predict component quality, alongside an expanded apprenticeship programme to support new roles like software developers and data analysts.
The result is a more than 100% performance improvement, enabling the Rugby site to hit record turnover and win additional contracts worth over £2m. The project also spurred a dedicated process development department, created a dozen new jobs and paved the way for a further £6.5m investment to implement two more connected production lines by 2027.
An AMRC spokesperson said the project demonstrates how industrial digital technologies can transform operations. The success has ‘set a new benchmark for fastener production processes’ and clearly shows the potential of technology-driven innovation in aerospace.
Process Improvements Within Constraints
While LISI’s collaboration showcases the benefits of innovation, industry-wide progress is often hampered by a reliance on established processes and materials. “The industry is built on aircraft and parts certified to specific production techniques, many of which were designed decades ago,” explains Andrew Mair, Chief Executive of the Midlands Aerospace Alliance (MAA).
While this reliance on legacy methods may limit flexibility in core manufacturing processes, there’s significant scope for improvements in areas that run parallel to assembly. Upgrading to integrated software platforms for production planning, resource management and inventory tracking, for example, is an area where many smaller manufacturers lag, yet can unlock substantial efficiency gains. Similarly, using robotics and automation to move materials or load machines can streamline operations and reduce manual labour and downtime.
Design innovations also hold promise. Advances in simulation and digital twin technologies allow suppliers to optimise components and assemblies before physical production, compressing design cycles and identifying potential issues earlier.
Generative design, where AI-driven software explores thousands of potential configurations, is helping create lighter, stronger, more cost-efficient components. Combined with additive manufacturing, suppliers can prototype and produce highly complex parts faster and, importantly, with significantly less waste than traditional ‘subtractive’ machining.
For instance, Airbus and Autodesk have used generative design and additive manufacturing to produce the world’s largest 3D-printed cabin component. Inspired by cellular structures and bone growth, the latticed partition to separate the passenger cabin from the galley is structurally as strong as conventional designs but 45% (30kg) lighter. When scaled to the entire cabin, Airbus estimates that the new design approach could save up to 465,000 metric tonnes of CO2 emissions a year.
Government Backing Fuels Further Investment
Recognising the transformative potential of advanced technologies, recent government announcements are geared towards accelerating adoption. One such initiative is the expansion of Made Smarter, an industry-government programme aimed at helping SME manufacturers adopt technology and build digital skills. Since its 2019 launch in the North West, Made Smarter has engaged with 2,500 manufacturers, funded over 330 technology projects, created more than 1,500 jobs and upskilled nearly 2,800 workers.
Its upcoming national rollout to all nine English regions by 2025/26, followed by Scotland, Wales, and Northern Ireland in 2026/27, will extend those benefits to thousands of manufacturers across the UK.
“The programme has proven the value technology and digital skills can bring,” says Donna Edwards, Director of Made Smarter NW, who described the national roll-out as “a huge vote of confidence in the contribution SMEs make to UK manufacturing.”
Additionally, the government’s announcement of £975m to extend the Aerospace Technology Institute (ATI) programme to 2030 was welcomed – although many favoured a longer-term commitment. With matching industry contributions, the funding will exceed £2bn, providing critical support for ultra-efficient and zero-carbon technologies.
“This support for R&D is crucial at a time the sector is ramping up rates to meet today’s demand while delivering ambitious technology programmes to bring next-generation aircraft technologies to reality,” says Gary Elliott, CEO of ATI.
Plotting a Sustainable Flight Path
The UK is making significant strides in sustainable aviation. The latest development saw a new Sustainable Aviation Fuel (SAF) mandate come into force on New Year’s Day. The mandate requires that 2% of UK jet fuel demand be met by SAF, rising to 10% by 2030 and 22% by 2040—delivering up to 6.3 megatons of carbon savings annually.
The mandate will be bolstered by the introduction of a revenue certainty mechanism to de-risk investments in new SAF plants and provide the confidence needed to scale domestic production.
The potential of hydrogen-powered aviation is also gaining momentum, with Russ Dunn, GKN Aerospace CTO, recently named as the new chair of the Hydrogen in Aviation Alliance. The HIA’s first major report, published in 2024, outlined a clear roadmap for industry and government to drive adoption. Yet, realising this vision requires more robust support for R&D, particularly within the manufacturing supply chain.
Andrew Mair explains that nearly all the R&D support currently goes to large corporations or start-ups, leaving the existing supply chain underserved. “We need more regionalised support, particularly for clusters like the Midlands Aerospace Alliance, to ensure small companies get the backing they need.”
Srimoolanathan of ADS underscores that aerospace is uniquely positioned to deliver immediate and long-term benefits for the UK economy. “The backlog presents an opportunity for short-term growth, job creation and technological advancement,” he says.
“But this hinges on balancing the immediate demands of today with strategic investments in areas like zero-emission technologies. With sustained support, the UK can maintain its position as a global aerospace leader while delivering tangible economic and environmental benefits.”